New
technology of "Angara-M" reusable launch vehicle family
development
(based
on picking up of I stages of reusable boosters by helicopter)
(see
detailed version of article in "Cosmonautics news" magazine
No.3, 2002)
Contents
Starting from
1999 Khrunichev State Research and Production Space Center together
with Mil Moscow Helicopter Plant (MHP) and "Parachute manufacture"
scientific research institute review a possibility of development of the "Angara"
first stages LV family on the universal rocket module basis. These
stages are rescued by the helicopter picking up that permits to
transform the "Angara" single use LV family into the reusable
LV family.
Thanks to using the new conceptions of reusability and new technical
solutions, covered by patent, the integral parameters of the above
reusable LV family will exceed the given level of the perspective
home and foreign reusable transportation space systems even at the
negligible required resource of the reusable boosters equal to only
5 launches.
The following features characterize the main dignities of the "Angara"
reusable LV family which is under development now:
- payload large
spectrum (light ones - up to 3.5 t, middle ones - up to 13.5 t,
heavy ones up to 23.75 t);
- short terms
of project realization;
- low cost
of research and development works;
- high succession
with "Angara" single LV family;
- use only
of available and tested systems, technology and materials;
- safety including
ecological one.
Khrunichev State
Research and Production Space Center develops the LV family in frames
of the "Angara" project, the main chain of which is the
universal rocket module (URM). URM is the basis for the LV boosters
construction. The stages consist of one, three or five above boosters
depending on the LV load-carrying capacity (see Fig. 1).
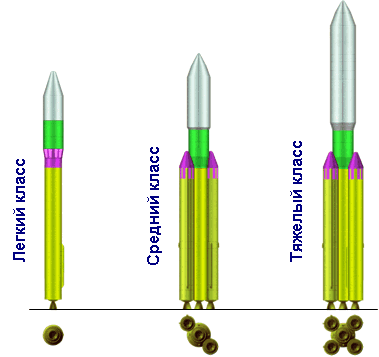
Fig. 1
Table
1
|
Light
class
|
|
|
Lift-off
mass, t
|
|
|
|
Payload
mass in low orbit, t
|
|
|
|
The development
of technology of reentry and reuse of more expensive parts (first
stage boosters) will improve considerably the "Angara"
LV family economic parameters. This technology will permit significantly
(in several times) to decrease the expenses for the payload injection
into space. Such technology is the economic advisable one in conditions
of the limited financial possibilities at using the technical solutions
which ensure the following:
- maintenance
and further development of step-by-step development strategy implemented
in "Angara" LV family;
- high dignity
with "Angara" base (single use) LV family;
- LV high flight
technical parameters;
- minimum expenses
for development and experimental testing;
- minimum technical
risk;
- safety (including
ecological one) of experimental testing and operation.
The means set
(hence-forth SET) development for ensuring the reusable use of the
first stage boosters may be the option of practical realization
of technology of reentry and reuse. The conception of this SET includes
the division of general task of boosters reentry into the following
specific tasks: braking in atmosphere, landing and transportation
to cosmodrome. In this case the relatively simple task of braking
is placed on the SET onboard part and landing and transportation
tasks - on its ground part.
As per the above conception the authors with consultation with the
leading specialists from Mil MHP and "Parachute manufacture"
scientific research institute developed the SET configuration. This configuration functioning
scheme (on "Angara-A5" LV example) is given in Fig. 2.
The SET onboard part arrangement is shown in Fig. 3.
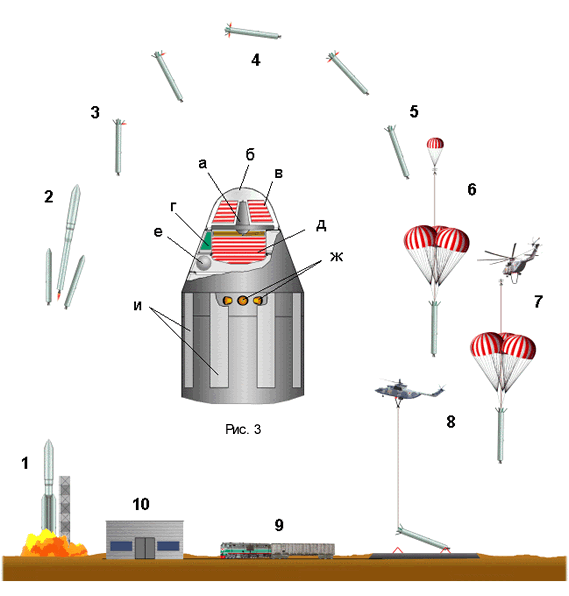
Fig. 2
The launch of
reusable boosters of 1-t stage as a part of LV (pos. 1 on Fig. 2)
is performed from the universal launch facility developed for the
"Angara" single use LV family.
As per the flight sequence after completion of their task the boosters
are separated from LV through 3.5 min after launch at velocity of
2820 m/sec (mass of each booster is equal to about 10 t at separation
moment) (pos. 2 in Fig. 2). Then the reactive control system is
ON (pos.3 in Fig. 2) and the stabilization flaps are deviated and
fixed in the open position.
During preliminary braking the reactive control system orientates
the booster within about 4 minutes that the tail compartment shall
be in direction to flight (pos. 4 in Fig. 2) and maintains this
orientation up to entering into the dense atmosphere (pos.5 in Fig.
2) where the booster orientation maintenance is realized due to
the stabilization flaps and booster braking - due to the flux effect
on the thermal protection of the tail compartment and stabilization
flaps. The boosters will descend up to altitude of 10 km within
about 6…7 minutes after separation from LV where their velocity
will be about 200 m/sec.
The scheme of the preliminary braking of the reusable booster is
given in Fig. 4.
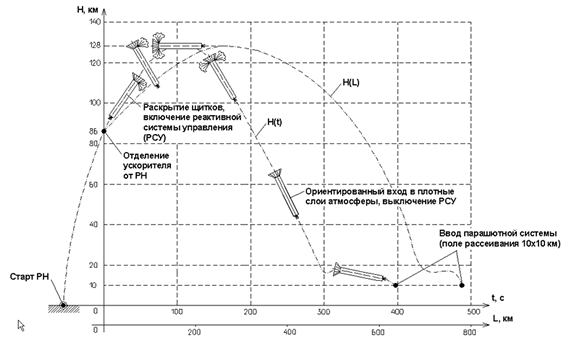
Fig. 4
H, km; Flaps opening, reactive control system ON; Booster separation
from LV; Orientated entering into dense atmosphere, reactive control
system OFF; Parachute system activation (impact field of 10x10 km);
LV lift-off; t, sec; L, km
The boosters
parachuting (pos. 6 in Fig. 2) starts at altitude of 10 km when
the parachute system is activated as per the barometric sensor.
The scheme of the reusable booster parachuting is given in Fig.5.
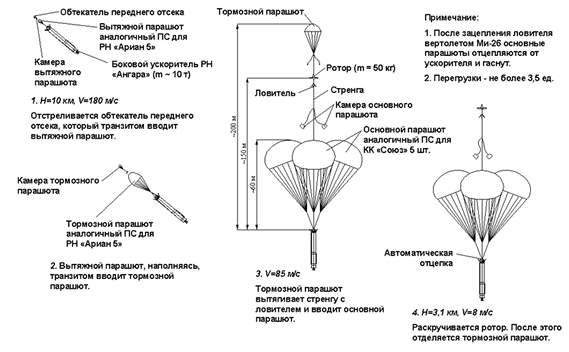
Fig. 5
Front compartment fairing; Pilot parachute like parachute system
for "Angara 5" LV; "Angara" LV (m 10 t) booster;
Pilot parachute chamber; 1. H=1- km, V=180 m/sec. Front compartment
fairing is jettisoned and takes out the pilot parachute; Pilot parachute
chamber; Brake parachute like parachute system for "Angara
5" LV; 2. Pilot parachute takes out brake parachute; Brake
parachute; Rotor (m=50 kg); Catcher; Strand; Main parachute chamber;
Main parachute like parachute system for "Soyuz" SS (5
pcs.); 3. V=85 m/sec. Brake parachute takes out strand with catcher
and main parachute; Note: 1. After catcher catching by Mi-26 helicopter
main parachutes are released from booster and packed. 2. Overloads
- not more than 3.5 g; Automatic release; 4. H=3.1 km, V=8 m/sec;
Rotor starts its rotation. After that brake parachute is separated.
The pilot and
brake parachute systems are the light option of the existed PS developed
by "Parachute manufacture " scientific research institute. The main parachute system
has five canopies with area of 1000 m2 each and is the main PS of
"Soyuz" SS.
The boosters picking up (pos. 7 in Fig. 2) is proposes to realize
by helicopter at territory used for the impact zones of the single
use boosters of first stages of the "Angara" LV family.
The picking up means were designed during works on the SET project.
These means permit exclude the serial helicopters modifications
for the picking up task. The scheme of the reusable booster picking
up is given in Fig. 6.
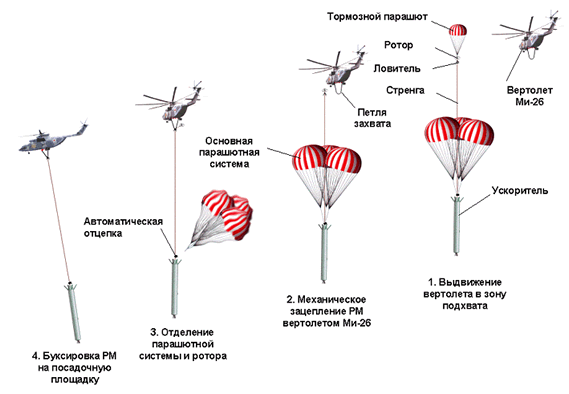
Fig. 6
4. Rocket module midair towing to landing area; Automatic release;
3. Parachute system and rotor separation; Picking up loop; Main
parachute system; 2. Rocket module mechanical catching by Mi-26
helicopter; Brake parachute; Rotor; Catcher; Strand; Booster; 1.
Helicopter flight to picking up zone; Mi-26 helicopter.
At the LV lift-off
the helicopters are at altitude of 3…3.5 km at boundary of the proposed
picking up zones which coordinates may be determined by calculations
before the LV launch. The picking up zones coordinates may be specified
as per the telemetry reading within 9.5…10.5 min from lift-off and
till the parachute system activation.
After parachute system activation the booster picking up zones are
specified again and their distribution between the helicopters is
realized. The picking up zones coordinate specifying may be done
as per the parachute system radio beacon signals.
The navigation satellite system on basis of the Russian Global Navigation
satellite system (GLONASS) and American Global Positioning System
(GPS) may be used for more accurate determination of the picking
up zones coordinated. These systems have the very high indexes of
the coordinates and velocity determination accuracy. Khrunichev
SRPSC has the experience of using the navigation system on the "Breeze-M"
upper stage. This system is based on the GLONASS/GPS satellite signals
receiver. It forms the navigation information frame and implement
it into the telemetry information current transmitted to the Earth.
The reusable boosters parachute within 8…9 min up to altitude where
their velocity will be acceptable for the picking up realization
and helicopters correct their position.
The helicopter crew detects the boosters in the picking up zone.
The helicopter equalizes the descending velocity with the booster
parachute velocity and realizes the booster mechanical catching
during manoeuvre in the horizontal plane. The scheme of the mechanical
catching of the reusable booster by helicopter is given in Fig.
7.
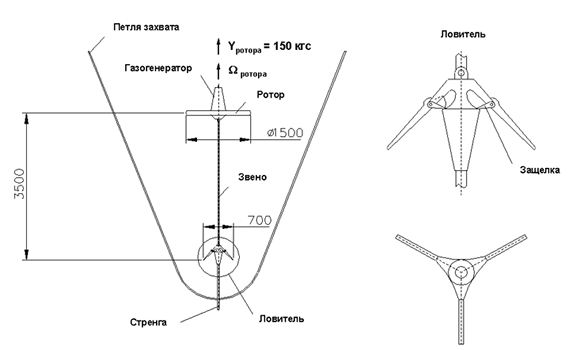
Fig. 7
Catching loop; Yrotor=150 kgf; rotor; Rotor; Gas generator; Chain;
Strand; Catcher; Catcher; Latch.
To make easier
the detection process it is possibly to use the "night vision"
devices, radio detection means, navigation satellite system etc.
That will permit, as expected, to realize the picking up in any
time of the day within wide range of the weather conditions.
It is proposed to realize the picking up in the manual regime at
the initial phase of the SET operation with the further its automation.
It is possible to use the target maintenance system for this.
The booster picking up probability will be not less than 80% as
per the preliminary estimation.
The following actions are foreseen for the helicopter and crew maximum
safety ensuring at the picking up operations realization:
- boosters
distribution at different altitudes due to individual adjustment
of barometric sensors as part of parachute system;
- using the
special destroying elements which ensure booster release from
helicopter at loads exceeded the permissible ones;
- using the
booster extraordinary release unit in case of emergency situation.
After the booster
mechanical catching by helicopter the booster parachute system is
released automatically and the booster is towed to the landing area
for putting to the ground and further release from helicopter.
The booster putting to the ground (pos. 8 in Fig. 2) is realized
as per the specially developed process which permits to avoid its
damage. The landing area may be located near the airport or railway
station.
The booster post-flight maintenance is carried out in the landing
area and includes the operations for the onboard systems OFF, external
inspection< preparation for transportation and arrangement in
the transportation container.
The boosters transportation to the cosmodrome (pos. 9 in Fig. 2)
may be realized by railway or by air.
The boosters pre-flight maintenance (pos. 10 in Fig. 2) may be done
at technical facility developed for the "Angara" single
use LV family.
To make easier the diagnostics the descending control system may
be equipped with means of data accumulation about environment acted
on the booster ("black box").
The LV transportation to the launch facility is realized on the
transportation-erection units developed for the "Angara"
single use LV family.
After each launch of the middle and heavy LV in order to decrease
the required resource of the reusable boosters it is proposed to
replace the "old" booster of the first stage on the new
one with the further using the universal rocket module of the replaced
booster as a part of the central unit which realizes the second
stage single use booster functions. Such replacement permits to
limit the required resource of the universal rocket module by 5
launches with corresponding profits in the flight technical parameters,
adaptability to manufacture, reliability and safety and to reach
the maximum possible economic efficiency.
The arrangement
analysis (see Fig.3 of "DESCRIPTION") showed the possibility
of the boosters equipping by the SET onboard part with the minimum
modifications of the universal rocket modules and ground support
equipment.
The scheme of the reusable booster preliminary braking (see Fig.
4 Схема предварительного торможения многоразового ускорителя (см.
рис. 4 of "DESCRIPTION") was reviewed during the scientific
and research work done as per the Khrunichev SRPSC order to increase
the impact zones for the "Angara" LV family first stages
single use boosters. The results of this work showed that during
the atmospheric descending the loads, acting on the booster, may
be decreased up to values, permitted for their reuse and boosters
impact areas may be decreased up to dimensions of 14х12 km.
The analysis of processes of the parachuted rocket booster catching
by Mi-26 helicopter (see Fig. 6 and 7 of "DESCRIPTION")
and its putting on the ground in the landing area, carried out by
the Mil MHP specialists together with authors and specialists from
"Parachute manufacture" scientific research institute
showed that the emptied boosters rescue means development may be
realized successfully at the financing presence. The official opinion
of Mr.A.G.Samusenko, General Designer of Mil MHP, is published in
"Cosmonautics News" magazine, No.3, 2003.
Now Khrunichev SRPSC carries out the scientific and research work
on the detailed investigations of parameters of the "Angara"
LV family first stages reusable boosters saved by the helicopter
picking up method. The work is on the finish phase.
The suggested
process of the emptied boosters descending and reuse will permit
to transform the "Angara" single use LV family into the
reusable LV family (see Fig. 1 and Table 1 of "Description")
by step-by-step increasing of the SET onboard and ground parts structure.
So the boosters equipping only by the SET onboard part will permit,
at least, to increase essentially the impact zones and simplify
the single use boosters utilization increasing the LV ecological
parameters. At the initial operation phase Set may be orientated
on the multiple using only one booster, for example, light LV with
lease only one helicopter. In this case the received additional
profits may be used for the SET development in full scope after
the expenses compensation (approximately through 5...10 LV launches).
The SET onboard part total mass will not exceed 13% of the single
use "dry" mass that predetermines the better flight technical
parameters for the reusable LV family which will be practically
identical ones to the same parameters for the "Angara"
single use LV family (see Table 1 of "Description").
The SET elements development and function main phases experimental
testing (including booster simulators parachute, their picking up
and putting on the ground in the landing area) may be realized with
the minimum expenses, in short time without waiting the LV and its
launch and technical facilities commissioning. The SET main feature
is the possibility of its flight tests during the LV launches with
commercial or federal payloads.
The SET development is connected with the minimum technical risk.
So the reusable booster loss during the tests or operation cannot
effect essentially on the SET commercial efficiency in general total
as its onboard part cost is insignificant. At the SET expensive
elements development (helicopters for boosters picking up) the domestic
techniques are used without modifications. These techniques are
in operation now and have a large experience of using. The boosters
use cycles number (up to 5) is quite reachable for today.
As per the preliminary estimation the SET operation cost will be
not more than 10% of the boosters manufacture cost that permits
to decrease the expenses in 2...3 times for the payloads injection
into space.
The suggested
process of the boosters descending and reuse is economic effective
one and may be realized in the short time including in the conditions
of the space rocket technology. At the same time the conceptual
and technical solutions, used in the suggested process, are perspective
ones in future as avoid the reusable LV from the systems and weight,
energy, processing and operation expenses, connected with these
systems which are unusual for it. The process elements may be used
for development of the reusable supply transportation vehicles for
the orbital space stations supply, payload rescue in the emergency
situations during the injection phase etc.
The objects
picking up has the large history of using. As per the "All
American Engineering" company information 1.5 mln. operations
of picking up the post containers with mass of 22.5 kg, different
cargoes with mass of 227 kg, airplanes with mass of up to 5.4 t
and gliders with mass of up to 8.2 t by airplanes and helicopters
were carried out within period of from 1938 till 1960s. The orbital
spacecraft, capsules, nose fairings, helicopters, airplanes and
other objects were picked up also. As per "Technol. Week",
1966, Sept., and "Aviation Week", 1966, Sept., No.11 and
12 the air picking up total number is 2 mln
As per "Technol. Week", 1966, 19, No.12, 32 and 34 "All
American Engineering" and "Pioneer Parachute" companies
realized the program of 5000 picking ups of the parachuted containers
with the artificial Earth satellites of the Samos and Discoverer
types. The above companies suggested to use the picking up method
for the TITAN IIIC LV stages , КК Gemini и Apollo SS with crew and
MOL piloted orbital station crew rescue .
The picking up systems reliability is high one. For example, as
per "Rech. Spatiale", 1963, 2, No.10 the probability of
the Samos intelligence AES parachute containers picking up by the
С-130В airplanes was 75-88%. As per "SAE Journal", 1965,
73, No.10 the projects of systems for picking up the parachuted
objects (LV stages, transportation SC, piloted AES etc.) (with mass
of up to 5450 kg with probability of 99%) by the Lockheed C-141
(Starlifter) airplanes were being developed in 1960s.
The picking up systems were used also in Russia. Gromov LII, Mil
MHP and "Parachute manufacture" NII developed and tested
the system of picking up the objects with mass of 300-500 kg by
the Mi-8T helicopter in 1984. But due to the financing absence all
further works were stopped.
|